CASE STUDIES
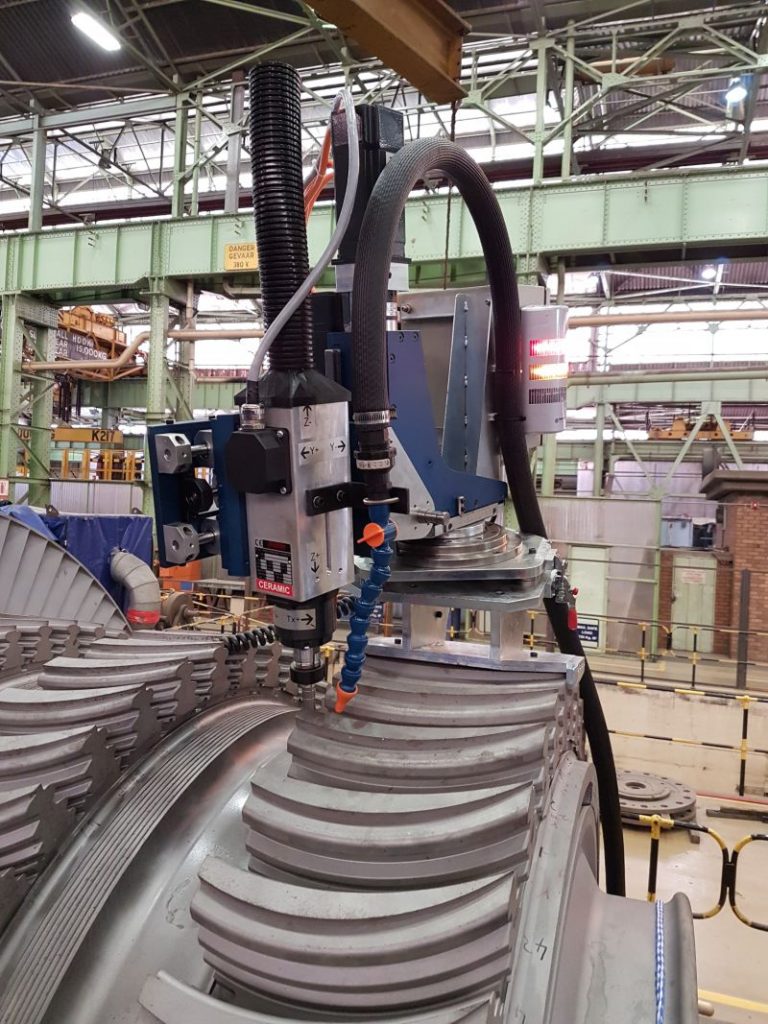
eNtsa Eskom Projects
Novel Sampling Technique for Through Wall and Complex Geometry Creep Damage Assessment
The nominal design life of power generation plant in South Africa has been exceeded at a number of stations. Decisions to safely operate the plant beyond the design life require careful assessment to allow accurate estimation of the remaining life of plant components. In South Africa creep damage characterisation of HTP plant components is predominantly performed by the Replica technique where more than a 100 000 replicas are taken annually. However, there are numerous areas of plant components which are not accessible for Replica inspection; due to complex geometry or limited access. An example of a complex geometry issue occurred where the creep condition at the 1st stage blade attachment area of a HP turbine rotor required assessment
Customised equipment (Weldcore®) was designed to perform the core sample extraction as well as the repair FHPP weld and is a combination of servo electric and hydraulic drives. The WeldCore® Sampling Procedure has to date been applied to four identical turbine rotors – three out of four rotors could be returned to service for a further 10 years after damage was machined away.
This intervention conservatively deferred capital expenditure estimated at R500M +
Turbine Rotor Serration Grinding as Removal and Preventative Technique to Stress Corrosion Cracking (SCC)
Stress corrosion cracking was identified on power station turbine rotors. SCC propagation rates suggest that if not addressed it may require major repairs or rotor replacement in the long term.
eNtsa has developed a technique to perform either preventative or crack removal serration grinding on all identified stages of the rotors. Preventative grinding can be used to reset the SCC lifetime back to day zero.
eNtsa performed preventative machining which negated the requirement to possibly ship the rotors out of the country. All the serrations on rotors were successfully machined over a period of twenty seven site days Estimated deferred Capital Expenditure R160M +
For more information about this technology, download the full project case study.
Engineering Support Unlocks R2M Green Energy Contracts for Student Start-up
Client: OKARA Energy [SME]
Assistance offered by eNtsa: OKARA Energy is start-up, launched in 2019 by two Nelson Mandela University engineering graduates. The pair aimed to provide engineering solutions in the renewable energy sector. OKARA identified that local wind turbines required maintenance to be performed, where torque arm bearings and pins needed to be removed and replaced. Previous attempts by local and international service providers resulted in damage to the turbine. eNtsa assisted OKARA Energy with a technical evaluation of the available engineering technologies, testing of the pin material and providing a conceptual design layout for the identified diamond-wire cutter solution, OKARA energy completed a function design, fabricated and iterated the diamond-wire cutter to be commercially operational. The result was a successfully completed contract, which led to OKARA Energy becoming the dedicated engineering service provider for a South African wind farm.
Deliverables: Technology evaluation, conceptual design, material test data and consultation.
Application Sector: Renewable Energy
Envisaged / Recorded Impact: Over R2m in contracts secured by OKARA Energy in 2019, and 5 jobs created.
OKARA secured a R1m contract with the local windfarm for the maintenance service in 2019, and has been appointed as the dedicated service provider to the windfarm. This appointment has further created opportunities for the company, including a new R1.1m contract in 2019 to perform oil services on wind turbines using custom equipment of their own design. OKARA is currently engaging with eNtsa as it explores new contracts within the renewable energy sector with an estimated value of R5m.
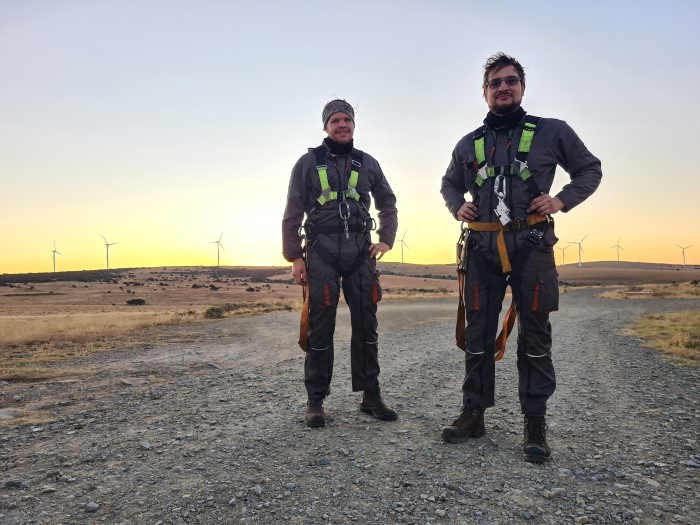
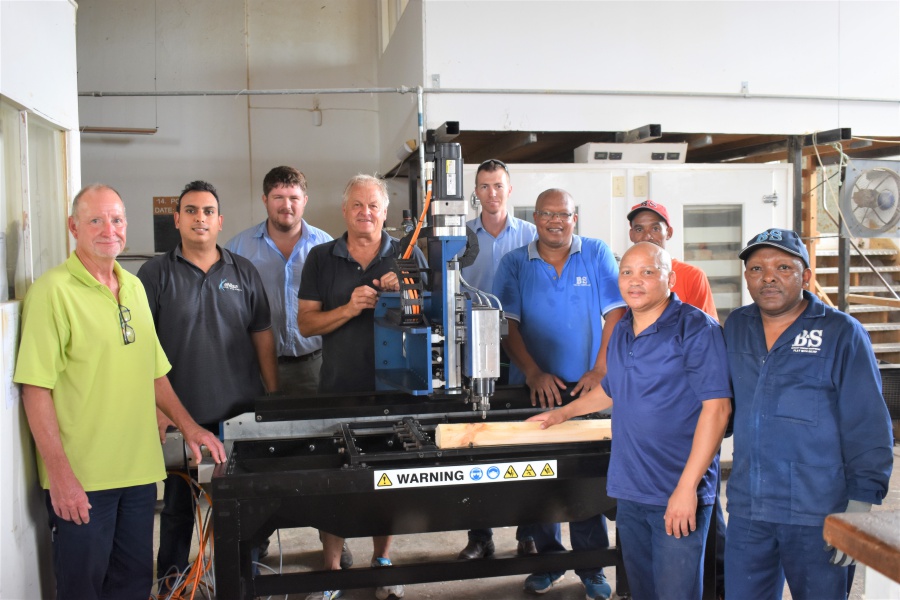
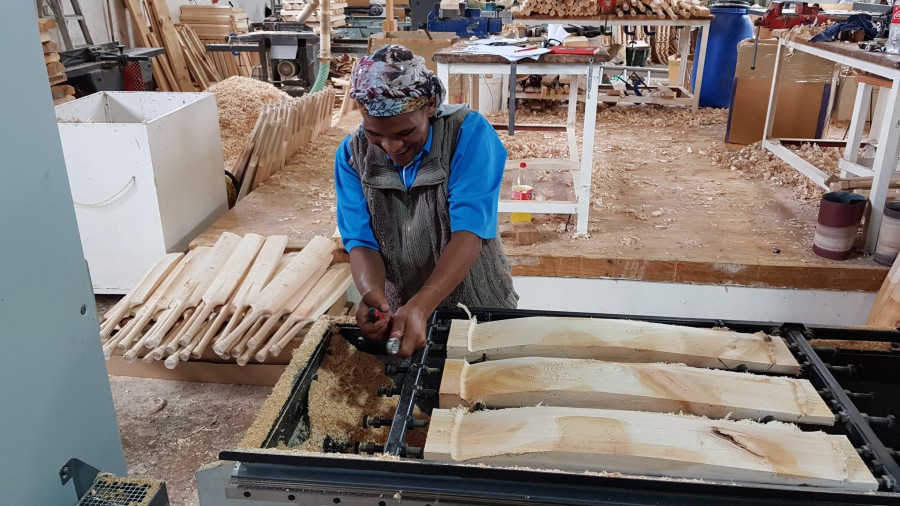
3-Spindle 3-Axis CNC Wood Router
Background
Bellingham and Smith (B&S) is a manufacturer of cricket bats based in Thornhill, Eastern Cape. They identified a need to increase the level of technology in their manufacturing process in order to gain the required export contracts to maintain/expand current workforce and access new markets. eNtsa developed a prototype 4-Axis CNC wood router in January 2018 (supported by DSI scale up funding). Since then, hundreds of bats have been machined on this system, with a daily outputs for the machine currently at 30 bats and increasing.
The client has indicated a need to continue scaling up their production capabilities with further custom machining to allow them to increase output and upskill their workforce.
The aim of this project was to develop a bespoke, industrial CNC wood router with three cutting heads to increase production and reliability.
In addition to improving productivity, by 127%, B&S indicated that the quality of the final product has improved, as bat shapes are consistent, and they have the ability to produce a wider range of shapes and sizes to supply a greater market. By increasing the overall capacity of B&S it has the potential to create employment for the Thornhill community, improve sustainability of the company and create opportunities in export markets.
B&S has begun upskilling staff to increase output demands, approx. 1000 bats produced in Feb/Mar 2020. B&S is currently negotiating new local and international contracts based on this new capacity.